Eni Indonesia; 7 Positions; 1 of 2 ads
Posting date: November 13, 2024 Expiry date: November 27, 2024
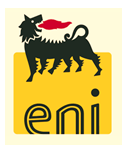
Eni is a major integrated international Oil and Gas Company based in Italy, with interests in 61 different countries, and employs approximately 30,000 people worldwide. Eni has Exploration & Production activities in Italy and other areas worldwide such as Africa, America, Asia Pacific, Eurasia, and the Middle East.
Eni in Indonesia currently holds participating interests in 10 (ten) Production Sharing Contractors (PSCs), which Eni serves as the operator in deep water areas with active exploration and development programs. The PSCs are spread across various locations in Indonesia, primarily in the Kutei Basin area. Eni’s portfolio in Indonesia demonstrates unique locations that reflect the company’s philosophy to operate in the core business and border areas to manage risks and achieve the best results in hydrocarbon discovery.
To support its progressive growth and build organizational capability, Eni in Indonesia is inviting candidates who possess relevant educational backgrounds, experiences, and competencies to join our company.
We are looking for qualified personnel with high motivation, initiative, and integrity to fill the following position:
Job Title: Liquids Scheduling Specialist
Purpose:
Coordinates operation and commercialization of liquids and gas production for Eni subsidiaries in Indonesia
General Accountabilities and Responsibilities:
Technical:
• Represent the Company at meetings with PSCs Contractors and Authorities to establish entitlement sheet calculation for the liquids lifting plan
• Represent the Company in the Joint Management Group to manage LNG and LPG Operations as well as to implement LNG and LPG SPAs
• Represent at all ship coordination meetings of Liquids and LPG as well as LNG entitlement and coordination meetings
• Implement Sales Purchase Agreement for all liquids and gas liftings, ensuring all export documents are in place on time and that all applicable regulations are followed
• Monitor and report all aspects related to the liquids transportation, storage, as well as marketing and lifting of the Company’s equity liquids entitlement
• Coordinate all internal/external parties (such as Buyer, Company’s OPs, terminal operator, Authorities, PPJK agent, Local shipping agent, Customs) to ensure smooth lifting activities
• Report liquids lifting realization to authorities, Company (Inatrade, Authorities, INSW, OSS, Finance, Operation, HQ, and others), and partners
• Report and communicate regularly to partners on entitlement and lifting plan
• Coordinate with the operator for the non-operated area
• Update the entitlement calculation as the basis for liquids to develop the lifting plan and annual revenue budget
• Monitor for and socialize changes to authorities’ regulations and terminal procedures and regulations that affect liquids liftings in Indonesia
• Check and approve invoices for surveyor fees and other costs arising from lifting activities
• Reports on official monthly Liquids, LPG, and LNG prices
• Monitor and prepare yearly over (under) settlement
• Provide input to internal on issues affecting the system: commercial drivers for Buyers; changes to facilities; domestic (pipe-gas) supply/demand, LNG, LPG, and liquids lifting operations
• Support the other activities of the Commercial & Business Development, working with and supporting other Company’s business function units as necessary.
• Comply with rules and standards set out in Company Policies, HSE Integrated Management System and Procedures, and personally demonstrate, develop, and disseminate a culture of safety and compliance with business ethics.
Qualifications & Experience:
• Education: A university degree in a relevant engineering or economics subject
• Professional Qualifications: Above 5 (five) years’ experience in exploration and production company in the international oil industry
• Language: Fluent in English and Bahasa Indonesia
Required Competencies:
Technical Competencies
Knowledge, Technical or Professional Skills:
- Liquids hydrocarbon commercialization
- Knowledge of gas sales/supply agreements and experience in LNG, LPG and pipe gas marketing is an advantage
- Specialist knowledge of government regulation on Liquids liftings
- Conversant with various types of agreements (JOA, PSC)
- Allocation and Lifting procedures
Non-Technical Competencies
- Negotiation and Commercial
- Communication/Relations Management
- Problem Solving
- Planning target control & Time Management
- Decision making
- Spirit of Enterprise
- Confidentiality keeping
Working Conditions:
Office Based with occasional business trips within Indonesia and to foreign destinations.
Job Title: Electrical & Instrument Technician
Purpose:
Responsible for providing technical advice and support to maximize the Operations efficiency of the Company's facilities. Electrical & Instrument activities will be conducted in a safe manner with maximizing field production efficiency while minimizing the total maintenance cost (production downtime, spare parts, manpower, etc.), and meeting daily production targets while complying with company guidelines and legal requirements.
General Accountabilities and Responsibilities:
• Provide electrical and instrumentation technical support to Operations and Maintenance teams.
• Proactively identify and develop ideas for improvements to the Electrical & Instrument system that can add value to the asset.
• Provide operations Electrical & Instrument input and support to future field development.
• Support design of Electrical & Instrument modifications to oil and gas plants and offshore floating facilities.
• Develop technical skills to improve capabilities.
• Participate in Root Cause Analysis for significant equipment failures.
• Develop operating procedures and guidelines.
• Managing relevant reporting and administration work based on the needs of the respective organization (including data recording, correspondence, etc. based on the function of this position).
• Coordinator of production engineering advice and support to maximize operation's efficiency.
• Assist in the preparation and maintain of the annual maintenance team budget.
• Demonstrate appropriate safety behaviors and commitment to environmental policies.
• Ensure maintenance activities are carried out in compliance with all relevant procedures and legal requirements.
• Using experience and knowledge to lead investigate and rectify operational and maintenance problems.
• Proactively analyze field data and develop action plans to improve maintenance performance that can add value to the asset through improved reliability and uptime.
• To ensure safe start-up and shutdown of process facilities.
• Progress all MOC (Management of Change) including gaining technical and budgetary approval and interfacing with facility and Project Engineering, ensuring that all changes to equipment design, type, or functions are controlled by application of applicable company Management of Change procedure.
• Develop Plant Maintenance Procedures and guidelines for all Company’s operation facilities.
• Ensure that all operation tasks are carried out according to the Company's established policies, procedures, and professional standards.
• Ensure appropriate risk assessments are carried out for all operation activities, with particular attention to recognizing the impact of change.
• Apply the lessons learned from design reviews, receiving inspections, and risk management findings and support team performance by sharing knowledge and best practices.
• Ensuring the confidentiality of the company's documentation.
Qualifications & Experience:
Education: Degree in engineering or technical degree.
Professional Qualifications:
• 5 years of Oil & Gas Industry experience
• Experience in the use of application of electrical and instrumentation simulation software and control system
Language: Fluent in English and Bahasa Indonesia
Required Competencies:
Technical Competencies
• Proficient in operation and maintenance of Gas Turbines Compressors and generators including support packages and ancillary equipment.
• Ability to use and develop PLC, DCS, and SCADA systems.
• Knowledge of oil and gas plant and offshore operations.
• Extensive experience and exposure to Root Cause Analysis and troubleshooting of operational equipment with state of the art diagnostic techniques.
• Experience in the design, installation, commissioning, maintenance,and troubleshooting of electrical, instrumentation and metering.
• Knowledge of subsea systems, ORF, and offshore operations is desired.
• Pre-commissioning, commissioning, and start-up experience.
• Production Operations: Maintenance Management, Predictive Maintenance,
• Operation/Maintenance Advising.
• Maintenance Engineering: CMMS Activities, Maintenance Engineering, Maintenance System Auditing, Maintenance Advising in Project Phase, Reliability/Availability. Analysis techniques knowledge, Maintenance systems, and policies knowledge.
• Organization Processes: Internal Standard, Feedback development and diffusion
• Technical Audit and Design Review, Documentation Management. Support and Technologies: Standard ISO, TQM and Quality System, Technical requirement and Standard.
• Compliance: Local/National and International Standard and Codes, Health, Safety, Environment, and Quality.
• Capable in terms of the maintenance management of Oil & Gas Platforms offshore or Onshore receiving Processing Facility.
Non-Technical Competencies
• Integrity & values
• Driving for results
• Value Creation Focus
• Teamwork & cooperation
• Initiative
• Analytical thinking
• Information seeking
• Concern for order
• Self-confidence
Working Conditions:
Offshore based (rotational)
Job Title: Flow Assurance Engineer
Purpose:
To provide specialistic engineering input to the project activities starting from the screening studies up to the completion of the execution phase, as direct performer and/or as monitoring/follow-up of the activities performed by others (i.e. contractors), and direct execution of Flow Assurance studies/analyses.
General Accountabilities and Responsibilities:
• Technical integrity of Flow Assurance design.
• Overall effectiveness and efficiency of Flow Assurance design.
• Capturing and dissemination of Flow Assurance engineering knowledge.
Key activities:
• Selection of the best technical/ economical solutions for a production facility.
• Flow Assurance of overall design integrity and compliance with international standards, company guidelines, and engineering best practices
• Supervising and directing Engineering Detail Contractors during the design, procurement, and construction activities, ensuring the quality of the works according to the contract requirements.
• Providing technical input, in line with project requirements, into technical studies and Basis of Design for onshore and offshore production and processing facilities.
• Ensuring a smooth and effective transfer of data and information between Contractors and between Contractors and the Company.
• Identifying and creating/ adopting appropriate Flow Assurance engineering standards, with due consideration of the environmental and logistic conditions of the equipment.
• Defining Flow Assurance requirements.
• Providing guidance & supervision to the 3D Model Review and related follow-on activities.
• Optimizing installation and construction activities/ sequences, minimizing cost and safety risks.
• Participating in process safety review activities.
• Acting as a technical authority on Flow Assurance issues for operational support.
• Participation in technical integrity activities and reviews/ audits.
• Train/ mentor junior engineers.
Qualifications & Experience:
Education: Bachelor’s Degree in Chemical or Mechanical Engineering or equivalent.
Professional Qualification:
• At least 3 years of experience in offshore and onshore Oil & Gas projects.
• Design experience concerning platform topside units / FPSO’s / subsea manifolds/ flexible umbilical/ flowlines and flow assurance studies on subsea pipelines including deep water.
• Preferably, participation in offshore/onshore operations, either for problem-solving or for commissioning / start-up.
• Preferably, participation in asset integrity and safety.
• Previous experience as a supervisor of engineering design contractors for offshore facilities / pipelines.
Language
• Fluent in English and Bahasa Indonesia
Required Competencies:
Technical Competencies
Professional Role general knowledge
• Flow Assurance
• Process Engineering
• Pipeline Engineering
• Asset Integrity
• Umbilical, Riser, Flowline
• Subsea Systems Design
• Instrum. & Telecomm. Systems Design
• Plant Design
Knowledge from other Prof. Areas
• HSE Principles and Systems
• Production Operations
• Asset Integrity
Business Line-Specific Skills
Upstream:
• Reservoir Management & Evaluation
• Drilling & Well Completion Activities
Non-Technical Competencies
• Knowledge and know-how: Analysis, Problem Solving, Results orientation
• Teamwork: Teamwork
• Passion - Setting an example: Positive attitude, Energy
• Courage to change: Flexibility / lateral thinking
Working Conditions:
Office Environment
.
Job Title: Marine & Logistic Superintendent
Purpose:
Responsible for overall marine operations and maintenance at West Seno/ Bangka facilities. The marine operation will be conducted safely by maximizing field production efficiency while minimizing the total maintenance cost (production downtime, spare parts, manpower, etc.) and meeting daily production targets while complying with company guidelines and legal requirements.
General Accountabilities and Responsibilities:
• Manage FPU vessel and tension-leg platform (TLP) marine operation & maintenance in accordance with local and international regulations, all associated vessel movements to support FPU and TLP operations and maintenance, logistic supply handling, helicopter handling, and control FPU’s mixed crude oil and condensate & ballast stability system.
• Ensure all offshore oil and gas Marine & Logistics activities are carried out in compliance with all relevant procedures, legal requirements, and the safe packing and handling of cargo to and from offshore locations
• Champion of supply of spares and stores
• Management and quality control of the computerized maintenance management system (CMMS) technical data and Planned Front
Line Marine Maintenance Routines held within the CMMS planned maintenance and material inventory control modules.
• Report Marine & Logistic activities to the Onshore Installation Manager (OIM) in a timely fashion
• Use experience and knowledge to lead investigations and rectify operational problems
• Proactively analyze field data and develop action plans to improve production performance that can add value to the asset through improved reliability and uptime
• Liaise with the control room, OIM, production supervisor, and related parties to ensure daily production targets are achieved
• Participate in the Champion of the Marine & Logistic Assessment Program and develop the Marine & Logistic Competency Assessment Module to minimize the skills and knowledge gap between Marine & Logistic operation team members as required by OPITO
• Produce comprehensive and accurate shift and crew change handover notes
• Ensure safe marine and logistic both underwater and subsurface support for start-up, normal shutdown, and abnormal/emergency shutdown of process facilities
• Progress all Management of Change (MOC) including gaining technical and budgetary approval and interfacing with facility and project engineering ensuring that all changes to equipment design, type, or functions are controlled by application of applicable company Management of Change procedure
• One of the key persons in handling vessel emergency on board FPU and TLP by organizing and managing emergency response team members not limited to people, plant, and environment
• Develop plant operation procedures and guidelines for all West Seno & Bangka (WSN & BKA) marine & logistic operation facility
• Ensure that all marine & logistic operation tasks are carried out according to the Company’s established policies, procedures, and professional standards
• Support established 2-year spare parts and ensure that material and equipment spare parts are optimized and available to minimize equipment downtime and unavailability
• Ensure appropriate hazard identification. Risk assessments are carried out for all operation activities with particular attention to recognizing the impact of change.
• Ensure that all planned and front-line marine maintenance tasks associated with equipment and facilities structure are considered and that all opportunities to minimize downtime of equipment are investigated to deliver maximum value
• Integral member of the pre-commissioning, commissioning, and start-up teams for the Offshore WSN & BKA Complex
• Apply the lessons learned from design reviews, receiving inspections, and risk management findings and support team performance by sharing knowledge and best practices
• Focal point during simultaneous operations (SIMOPS) activity
• Manage MEG, Diesel Fuel, and Fresh Water transfer to and/or from boats
Qualifications & Experience:
Education: Bachelor’s degree in Class-1 Marine Engineer or Engineering, Mechanical Engineering in any relevant subjects
Professional Qualifications:
- 7 (seven) years of oil & gas industry experience
- Have worked as chief engineer in the oil & gas industry foreign going vessels for at least 1 (one) year or hold the certificate of competency as Master Mariner Unlimited Class-1 and have commanded foreign going vessels with capacity over 3000 GRT for at least 1 (one) year
Language: Fluent in English and Bahasa Indonesia
Required Competencies:
Technical Competencies
• Extensive knowledge of ship offshore floating production engineering and floating production operating systems.
• Extensive experience and exposure to Root Cause Analysis and troubleshooting of marine operational equipment with state-of-the-art diagnostic techniques.
• Experience in maintaining maritime vessels, and offshore supervisory or managerial background is desirable.
• Knowledge of subsea, subsurface system, Custody Metering System, ORF, and offshore operations desired.
• Marine engineering Pre-commissioning, commissioning, and start-up experience
• Production Operations: Maintenance Management, Predictive Maintenance, Troubleshooting Maintenance Operation/Maintenance Advising
• Maintenance Engineering: CMMS Activities, Maintenance Engineering, Maintenance System Auditing, Maintenance Advising in Project Phase, Reliability/Availability analysis techniques knowledge, Maintenance systems and policies knowledge
• Organization Processes: Internal Standard, Feedback development and diffusion, Technical Audit and Design review, Documentation Management
• Support and Technologies: Standard ISO, TQM and Quality System, Technical requirement and Standard OCIMF, ISGOTT, IMO, IMCA, and Classification Bureau
• Compliance: Local/National and International Standards and Codes, Health, Safety, Environment, Quality, underwater diving, subsea, subsurface
• Capable in terms of the maintenance management of Oil & Gas Platforms offshore or Onshore receiving Process Facility
Non-Technical Competencies
• Leadership skill
• Safety behavior
• Integrity & values
• Driving for results
• Value Creation Focus
• Teamwork & cooperation
• Analytical thinking
• Information seeking
• Concern for order
• Self-confidence
• Team player
• Initiative
Working Conditions:
Offshore based (Rotational)
Job Title: Senior Petroleum Engineer
Purpose:
Coordinate and supervise the petroleum engineering team assuring the production and completion optimization through suitable actions and the correct management of the recorded production data
General Accountabilities and Responsibilities:
• Follow up the drilling and production surveillance activity
• Planning well-testing acquisition and follow up the execution
• Interface with operated and non-operated reservoir teams suggesting well interventions to optimize the well performance and to ensure the correct field implementation and execution
• Participate in the preparation of well drilling programs and plan the acquisition of the dynamic data
• Contribute to identifying possible actions to ensure maximum efficiency in the optimization of well production ensuring technical quality and cost-effectiveness of the solution adopted
• Analyze and interpret the well test and production data collected at the well site, ensuring their QC
• Contribute to the preparation of documents relevant to the work over and production activity
• Propose and introduce new technologies aimed at improving well performances, field recovery, and economics
• Identification of the formation damage problems
• Provide the necessary support to operated and non-operated reservoir teams related to Production Optimization programs including main stimulation techniques (fracturing and acid stimulation), Well performance analysis, well test design and interpretation, and reservoir drive mechanism analysis
• Monitor production activities, analyzing production data, to verify compliance with forecasts and propose the necessary actions in order to ensure a cost-effective reservoir management.
Qualifications & Experience:
Education: Petroleum Engineering, Reservoir or Engineering related disciplines
Professional Qualification: Minimum 10 (ten) years within the oil & gas industry with Reservoir Geology, Geophysics, and/or Reservoir Engineering experience. Team lead experience preferred.
Training and Courses:
• Petroleum & Reservoir Engineering
• Subsurface
• Assets Management
Languages: Fluent in English and Bahasa
Required Competencies:
Technical Competencies
- General understanding and experience with Reservoir disciplines - geology, geophysics, petrophysics, reservoir and petroleum engineering.
- Advanced knowledge and skill in Petroleum Expert Package and OFM. Petrel and/or Eclipse software experience preferred.
- Analytical and statistical analysis and assessment of uncertainty
- Advanced competency in Microsoft Office (with emphasis on Excel and PowerPoint)
- In-depth understanding of the oil industry and resource development
- Experience and understanding of Eni processes and Eni corporate standards.
- Good command of spoken and written English
Non-Technical Competencies
- Strong Leadership and team building
- Problem solving & Analytical skill
- Decision Making & Strategic Thinking
- Communication
- Negotiation
- Listening and reception
- Excellence orientation
Working Conditions:
Office environment
Job Title: Interface Coordinator
Purpose:
Managing all joint venture (JV) aspects of the Asset involving Exploration, Development,
Production & Decommissioning activities with JOA as the protocol. The objective is to deliver the strategic growth of asset against the equity (expenditure forecast, performance monitoring, and analysis), creating added value to the portfolio and to consider potential risk exposure while maintaining productive collaboration among the JV Partnership. Managing projects internal and external interface including with authorities.
General Accountabilities and Responsibilities:
• Participate/represent at partnership meetings including operating, technical and
management committee meetings, as appropriate, and manage partner relations.
• Support the coordination of JV activities including multi-functional support of JV
Business Processes (e.g., JV approvals – Budgets, AFE’s, FM’s, Contracts); technical proposals submitted by Operators.
• Oversee the operated assets activities from all business perspectives (Technical, Commercial, Legal, Financial, HSE) in coordination with the Business unit and Head Quarter functions.
• Update and monitor the activities/operations on a periodical basis as appropriate; Manage and influence relationships with Partners’s area facility owners and users; Ensure agreements & business practices are compliant and current and ensure compliance with internal and external (authority); JV plans and forecasts (OPEX/CAPEX, production, maintenance, HSE, Decommissioning).
• Participate in negotiations on JV matters and provide support to other functions/ team members; continually identify opportunities or key drivers to increase value of the asset; Provide business insights to the JV to ensure awareness and focus on internal business delivery.
• Support reporting of the activities/operations on a periodical basis as appropriate to the Authorities; ensure compliance with internal and external (authority) requirements; Prepare and present to Authorities of plans and forecasts (CAPEX, project’s production, maintenance, HSE, Decommissioning aspects).
Qualifications & Experience:
• Education: Bachelor’s degree in relevant Engineering of technical disciplines.
• Professional Qualification: Minimum 5 Years Experience in the Oil and Gas Industry, preferably experience in Project Management.
• Training and Courses:
• Economic Analysis
• Local PSC and Government Regulations
• Advance Negotiation Skills
• Communication Skills
• Project management
• Internal Audit
• HSE Awareness
• Language: Fluent in English and Bahasa Indonesia
Required Competencies:
Technical Competencies
- Project management
- Knowledge of PSCs requirements
- Knowledge of JOAs requirements
Non-Technical Competencies
- High Level of confidentiality
- Interpersonal skills, both written and oral communication
- Negotiation skill
- Decision making
- Relation management
- Problem solving
Working Conditions:
Office Environment
Job Title: HSE Management System Senior Specialist
Purpose:
To provide assurance of sustainable implementation of the Company HSEQ management system as well as ensuring compliance with regulation, Company requirements, and industry practices by performing continuous monitoring and evaluation, including the audit process and provision of advisory/consultancy.
General Accountabilities and Responsibilities:
• Assure the validity and accuracy of the HSEQ Management system through continual improvement approaches. Including process to facilitate the development of HSE procedure and maintain its availability and applicability in the Company.
• Support implementation of the HSEQ Management System, including but not limited to the scopes of:
- HSEQ Management System at the Operation stage
- Contractor HSE Management System
- HSEQ Management System at Project and Development, including SIMOPS, Drilling and Exploration activities
- Energy Management System
• Facilitate the HSE program execution to sustain the HSE performance, such as HSE Campaign; Behavior Base Safety; and HSE Training.
• Continuously review the performance of the HSE Management system, including the HSE KPI, either through regular monitoring and evaluation; inspection programs; and HSE Audit programs.
• Evaluate HSEQ compliance with regulations and Company requirements and policies.
• Provide support and advise to project/operation/exploration/drilling team on implementation of HSEQ management system aspects.
• Provide support in coordination of implementation of the Company’s HSE MSG, ISO 9001, ISO 45001, ISO 14001, and ISO 50001 Management Systems.
• Provide support in development and maintaining the HSE competency requirement.
• Participate in investigation of non-conformances/incidents.
• Participate in Emergency Response Team.
• Provide support in development of Company HSEQ 4-Year Plan and Annual Plan/Budget, especially in related to management system implementation and development.
• Facilitate the development, implementation, and monitoring of HSEQ Plan on HSE-MSP (Management System and Performance) aspects, including the concept of HSE program for Indonesia and site level.
• Comply with requirements of the Health, Safety, and Environmental laws of Indonesia and conform with Company’s corporate policy on Safety, Health, and Environment aspects.
Qualifications & Experience:
• Education: Bachelor in Relevant Degree (preferably in Engineering Degree)
• Professional Qualification:
- 5-7 years of experience in HSE (preferably in the Oil & Gas Industry)
- Professional Skill: HSEQ Management System, HSEQ Audit, HSE Risk Management, HSE Prevention & Protection, and Regulatory Requirement
• Training and Courses: preferably to have attended : Lead Auditor Course and NEBOSH - IGC
• Language: Fluent in English
Required Competencies:
• Technical Competencies
- Comprehensive understanding on HSEQ
- HSEQ Management System
- ISO 14001, ISO 45001, ISO 9001, and ISO 50001
- Incident Investigation process
- Continuous Improvement
- Auditing skills
- Risk Management
• Non-Technical Competencies
- Analytical Skill
- Problem Solving
- Team Work
- Facilitator and Communicator (stakeholder engagement)
Working Conditions:
Office Environment, with visits to Onshore/Offshore Site (as necessary).
Should you are interested in the position & meet the qualifications required, please send only your latest resume (in MS Word or PDF format with a size no more than 1 MB) to:
Recruitment.id@eni.com
Please mention the position title in the email subject: Apply for (position title)
Please note that applications may not be reviewed if received after 22 November 2024. Only shortlisted candidates will be notified.
Please be aware that Eni will never ask the applicant to pay any fee or appoint any travel agent for the selection process. All communications that ask the applicant to pay any fee or use a specific travel agent are fraudulent & scams. The application can only be sent through the above email.